As the traditional LED industry enters a mature saturation period, manufacturers have adjusted their development strategies, and instead expanded segments such as automotive lighting, plant lighting, UV LED, IR LED, as well as small spacing, mini/micro LED and other new display fields. Among them, in the field of UV LED, although many manufacturers have long -term layout, the UV LED product market has not received high acceptance in the past. Therefore, the UV LED industry has been in its infancy, especially the UVC LEDs with relatively high technical difficulties and prices. However, since the new type of coronary virus pneumonia has spread globally, consumers' awareness of sterilization and disinfection has increased rapidly, and the demand for UVC LED series products has increased, promoting the global multi -party forces to invest in the research and development of UVC LED technology, which has also spawned various kinds of various kinds Products, how do these products meet the relevant requirements? In fact, many factors need to be considered in the selection of reliable UVC LED products, such as: different doses and irradiation time for different viruses and bacteria to achieve disinfection and sterilization effect. From the perspective of product production, there are many considerations from the extension chip to the packaging to the finished product. This time, LEDINSIDE has revealed the required materials, craftsmanship, technical problems and development trends required for the UVC LED packaging session to better understand the UVC LED packaging product. UVC LED encapsulation forms, craftsmanship, and material selection are special. At present, UVC LED packaging has three forms: organic packaging, semi -inorganic packaging (also known as“Near -inorganic packaging”) And all -round packaging. Organic packaging uses organic materials such as silicone, silicon resin or epoxy resin, mainly including LAMP, SMD, ceramic MOLDING and other products. The overall technology is relatively mature, but the anti -ultraviolet performance needs to be further improved. Half -inorganic packaging (also known as“Near -inorganic packaging”) Use organic silicon materials with glass and other inorganic materials. The whole inorganic packaging avoids the use of organic materials throughout the process. The combination of lens and substrates is achieved by laser welding, wave welding, and resistive welding. Effectively improve the stability and reliability of UVC LED devices. It is understood that domestic manufacturers such as Guoxing Optoelectronics, Mustang Shen Zi Zi, Hongli Bingyi, and Huayinxin have all developed the UVC LED products of all -inorganic packaging. At present, the semi -inorganic packaging product is still the mainstream of the domestic market. It is mainly composed of a ceramic stent and quartz glass with a cup. It is placed by coating the anti -ultraviolet glue in the edge area of the ceramic substrate to achieve the lens. Specifically, dot glue at the top or steps of the cup, and then cover the quartz glass for curing and bonding. In terms of materials, UVC LED packaging is different from ordinary LED. First of all, the choice of quartz glass is because quartz is inorganic, will not be affected by ultraviolet rays, and the high rate of quartz glass on the UVC band is high. Secondly, in terms of heat dissipation substrates, due to the low efficiency of UVC LED photoelectric conversion, most of them are converted into heat, so the aluminum nitride heat sink substrate with high heating rate is generally used. In addition, UVC has a bad effect on glue. Therefore, the requirements for UV resistance in the glasses of bonding glass and brackets are higher than that of ordinary LED packaging. It is also worth noting that some manufacturers use aluminum oxide heat dissipation substrates. Both aluminum nitride and aluminum oxide substrates belong to the ceramic substrate. The main difference between the two is that the heating rate of aluminum nitride is much higher than alumina. Among them, aluminum nitride thermal conductivity is generally about 140W/mk-170W/mk, while aluminum oxide thermal conductivity is only about 30w/mk. Alumina ceramics are generally white, low thermal conductivity, usually used for low -power products. However, alumina ceramics is large, and it is easier to crack than aluminum nitride. Therefore, it is prone to collapse in the process of cutting. Aluminum nitride ceramics generally presents gray -black, has a high heating rate, and is usually used for high -power products. In addition, there are also alumina ceramics doped on the market, which are also gray -black, but the heating rate is lower. The quality of thermal management and gas -density affects the quality of UVC LED packaging products UVC LED packaging products. The quality of the quality of the product and the influence of gas tightness. These two aspects are also technical difficulties in the packaging link. Among them, thermal management directly affects the life of UVC LED packaging products, while gas tightness determines its reliability to a large extent. UVC LED is sensitive to heat, its external quantum efficiency (EQE) is low, and only a small part of the electrical energy is converted into light, and most of the electrical energy is converted into heat, which directly affects the service life of the chip. In view of this, at this stage, many products are based on the scheme of pouring chips with high heat -conducting aluminum nitride substrates. Aluminum nitride has excellent thermal conductivity, can tolerate the aging of UV light sources itself, and meets the needs of UVC LED high -heat management. In addition to materials, the packaging process is also the influencing factor of heat management. The packaging process is mainly reflected in solid crystal technology, including silver pulp welding, tin paste welding, and gold tin co -crystal welding. Although silver pulp welding is good, it is easy to cause silver migration, resulting in the failure of the device. As for the welding of tin paste, because the melting point of the tin paste is only about 220 degrees, after the device patch, the phenomenon of re -fusion will occur again. Golden tin co -crystal welding is mainly used for co -crystal welding through the welding agent, which can effectively improve the binding strength and thermal conductivity of the chip and the substrate. In contrast. Therefore, the gold tin co -welding method is used on the market. In the welding process, it mainly involves the problem of welding hollow rate. Welding empty hole refers to the defects formed during the welding process of LED chips and substrates. It presents a state of empty appearance in appearance. It is an important indicator affecting heat dissipation. The lower the welding empty hole, the better the heat dissipation effect, the longer the product life, the better the quality, the better the quality. It is understood that the inorganic packaging technology of Huayin core uses inert gas and restore gas mixed protection environment to perform hot pressure co -crystal welding of the chip to further increase the efficiency of electrical connection, while reducing the hollow rate, stable LED knot temperature. Guoxing Optoelectronics's advantages and characteristics in common crystal welding technology are very prominent. The company has 10 years of common crystal technology precipitation, and the reflux common crystal vacuum rate is basically controlled within 10%, which is greatly lower than similar products on the market on the market. According to reports, in terms of reducing welding hollow rates, the company has formed a relatively leading and perfect process technology. At present, the overall empty hole area of its UVC LED products is below 10%, and the largest empty hole area of a single hole is below 2%. Compared with the hollow rate of the same type of product in the market 15%-30%, the heat dissipation effect is excellent, the product life is long, the product item products Better control. In terms of reliability, the form of packaging is one of the factors, but the key is. In the form of semi -inorganic packaging, glass lens and cup ceramic substrates will form a closed cavity through glue connection. Because the closed cavity cannot be vacuum, when the glue is heated, the air in the cavity is vulnerable to heat and spilling, forming a bubble, and a gas channel formed in severe cases. At this time, external water vapor and impurities can enter the product through air bubbles and gas channels, which cause pollution to chip and substrates and other materials, which seriously affects the gas tightness of the product, thereby affecting the light and reliability. It can be seen that the impact of gas tightness has a great impact on the quality of UVC LED packaging, and process processing technology is very critical. It is worth mentioning that by optimizing the surface treatment and continuous packaging and curing technology of the substrate, the National Star Optoelectronics has also formed a complete packaging process solution, which can effectively reduce the closed cavity air, realize the zero air bubble and zero of the UVC LED device, and zero zero. Air passage. UVC packaging pattern: semi -inorganic packaging is the main, and the whole inorganic packaging is supplemented by thermal management and gas tightness. UV resistance is also one of the technical difficulties of UVC LED packaging. In order to improve the anti -ultraviolet performance of the product, many manufacturers have stepped up the development of all -inorganic packaging products. For example, Guoxing Optoelectronics has developed high -cost all -inorganic UVC devices for special products, and the cost advantage is obvious. At the same time, the company is also jointly developing anti -UVC fluoropic resin packaging material products with material manufacturers. The product has the characteristics of high temperature resistance, larger current, and anti -UV radiation. Jingneng Optoelectronics's UVC LED products are mainly high -power ceramics packaging. Ceramic materials are packaged, and product heat dissipation performance is good. Hongli Zhihui also continues to carry out research on inorganic packaging technology, which aims to develop UVC LED products with high light power, high reliability, long life, and cost -effectiveness. In terms of UVC LED packaging future development trend, Guoxing Optoelectronics believes that the domestic market will still be mainly encapsulated in the next year or two, supplemented by the whole inorganic packaging, but as organic materials have improved and innovated by UV resistance and innovation , Organic encapsulation such as fluorine resin will likely occupy a part of the market share. Since the beginning of this year, different technical fields of UVC LED have achieved certain breakthroughs, conveying signals that the industry is booming. Although, due to high cost and low light effects, the current UVC LED products cannot completely replace medical sterilization UV mercury lamps. But Guoxing Optoelectronics believes that with the advancement of technology, I believe that UVC LED will slowly enter this market soon. Moreover, due to small volume and simple design, UVC LED is currently in the field of mobile killing and small space sterilization. Compared with mercury lamps, it has certain advantages. According to LEDINSIDE, from the current market application, UVC LED has begun to be applied to surface sterilization (carried sterilization products, sterilization lamps, maternal and infant products), water sterilization and air purification
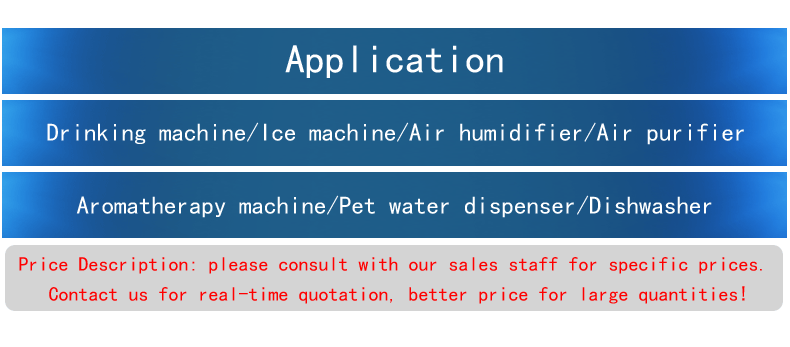